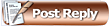 |
|

06-25-2018, 09:19 PM
|
|
|
Join Date: Jun 2007
Posts: 43
|
|
ICF Built Homes
Just wondering if someone on the forum may be familiar with Insulated Concrete Foundations or construction of this type. Looking for feedback on homes constructed this way and wondering the pros and cons of this type of construction. The house uses ICF from the foundation to the roof trusses, not the old stick built that I know. Just looking for thoughts / comments. Thanks in advance.
|

06-25-2018, 09:26 PM
|
 |
|
|
Join Date: Jul 2009
Location: GP AB
Posts: 16,250
|
|
I used ICF on all three houses I built in GP, but only foundation. Ideally going to the trusses is best, but it's hard to get your investment out on resale, seems like not everyone appreciates the extra cost and value.
I used Superform ICF, it's made in Pincher Creek (I actually did some work in the shop addition, and got to tour through and see production. Impressive). I think it is a premium product. Someday I may build again, and go up to trusses. If you are planning on staying in the house for a while, and don't flinch at the cost, do it. The energy savings, and how quiet they are (from outside noise) are awesome.
__________________
'Once the monkeys learn they can vote themselves a banana, they'll never climb another tree.'. Robert Heinlein
'You can accomplish a lot more with a kind word and a gun, than with a kind word alone.' Al Capone
|

06-25-2018, 09:29 PM
|
 |
|
|
Join Date: Apr 2008
Location: Alberta
Posts: 331
|
|
We have built a couple houses in the last 8 years and did ICF basements in both of them. If I were to build our "forever" home it would be ICF to the rafters!!! Sorry no personal experience on ICF to the rafters but if it is your "forever" home I would be looking at it really hard.
|

06-25-2018, 10:08 PM
|
 |
|
|
Join Date: Jan 2012
Location: 204
Posts: 5,450
|
|
My brother has one, and I’ve plumbed in a fair number.
Never heard complaints.
At my brother’s house you can’t tell a temperature difference from the basement to the main floor. (We roughed in floor heat but never hooked it up)
The only thing I’d worry about is the guys doing it. As long as they take care to make sure everything is straight it will be great. Apparently some guys think icf can only get mostly straight.
__________________
"I like to quote my own quotes" ~ Dewey Cox
|

06-25-2018, 10:46 PM
|
 |
|
|
Join Date: Feb 2010
Location: In the woods
Posts: 8,923
|
|
Done a basement in icfs and seen a few built to the roof with them. Fairly easy process and the extra insulation is hard to beat. Definitely not the cheapest method of building though but solid and as mentioned, very soundproof and not suceptable to temperature changes as easily as other forms of construction.
__________________
I feel I was denied, critical, need to know Information!
|

06-25-2018, 11:02 PM
|
|
|
Join Date: Jul 2012
Location: one Fort or another
Posts: 768
|
|
I studied those extensively for awhile, and watched a multi-storey commercial one go up. It's got several advantages including solid concrete walls from footing to rafters, permanent insulation, and a permanent form which doesn't have to be pulled away after curing. The forms can be set by hand, and pours done in a conventional manner.
Several things turned me off of it however. First, the concrete and insulation end up being in the wrong places - that means reversed. Optimally the main mass of concrete should be on the inside, close to inside air for thermal stability, rather than insulated from that inside air. Secondly, the insulation on the exterior always needs an additional protective coating of some kind from termites and other kinds of attack, both below and above grade. If an insulation band is created in the center of a concrete panel instead, the outer c/c wythe protects the insulation and can directly serve as a cosmetic surface. No further treatment or maintenance is ever needed on the exterior. The inner (thicker) c/c wythe is both the main structural one and the thermal mass to maintain a steady temperature. You'd use something like furring strips on the inside wythe to mount gyprock for fire protection, but the same is true for ICF styrofoam I'd guess.
Additionally, only rebar is used in the walls of the ICF building as is typically done in relatively fat foundations. But not pre-stressed cabling. So if you want to use some arrangement of panels where tension stress becomes very important, you need to use factory-built prestressed panels or very thick conventional walls. Typically panels would be used where they need to be very long, and/or have very large sideways forces against the wall without any additional interior support.
Further, the so-called zero-slump concrete used in factory trays, when cured under controlled conditions, is eventually stronger than site-poured watery wet-slump and has far fewer curing cracks. That's why long highway overpass bridges are factory-made in that manner together with prestressed cables.
Factory-made prestressed, insulated-core panels are laid down locally in perfectly flat, straight trays, with precision-laid window and door openings and electrical and plumbing conduit. It comes out in very precise dimensions much closer than you could ever get on site, and can be quality-checked even before delivery; so no surprises.
Finally, crane-erected c/c panel walls, floors and roofs go up much faster with much less labor. In this country labor costs are a very high percentage of total costs compared to materials. Lots of cranes are available in most areas these days too. At least where it would otherwise be necessary to bring in transit mix. So, better to save on labor and spend on precision materials.
So I'd obviously rather use factory-made prestressed insulated concrete panels erected by crane now, rather than ICF poured over multiple storeys with cold joints between each pour. Either ICF or panels are way better however than conventional chipboard and frame thrown together by hammer-bangers.
Last edited by Arty; 06-25-2018 at 11:14 PM.
|

06-26-2018, 09:57 AM
|
|
|
Join Date: May 2007
Posts: 3,964
|
|
Used 8" Advantage Block on an ICF walkout basement. R 27 on the 8 ".
Warm in winter but yes, you are required to use the adhesive membrane on the exterior, instead of usual tar seal on Concrete. It is VERY HARD to get an ICF basement to ever leak. Concrete pour with snap tie protrusions always are a source of future leaks, let alone cracks that form over time.
Still by far a better result. Crew is on site once, not twice, and the pour using a concrete pump is very even in the walls. Cross tie the Re Bar vertical and horizontal, and it is a far stronger foundation wall than any straight concrete form pour.
As for getting the money back, most home buyers can't tell the difference between simple preserved wood foundation and an ICF basement, so no, they won't pay more when comparing two houses side by side, but that is not why you do ICF in the first place.
Drewski
|

06-26-2018, 10:32 AM
|
 |
|
|
Join Date: Apr 2018
Location: Calgary
Posts: 1,818
|
|
I like ICF for many reasons already stated. My opinion is also based on how I see residential crews in my area install conventional concrete. Pouring in sub zero temperatures with no heat and removing forms the next day. Cold joints. High slump and little vibration. Not pouring footings on native soil or properly compacted base. Good enough for a house I suppose, but not to code and way less longevity, strength and crack resistance than if done properly. It also dismays me to see how many sunken porches and driveways are out there. Proper compaction doesn't seem to be a high priority. There are obviously exceptions, but the pressure to do it cheaper is there in most cases.
|

06-26-2018, 10:35 AM
|
|
|
Join Date: Jan 2018
Posts: 87
|
|
Quote:
Originally Posted by Drewski Canuck
.
As for getting the money back, most home buyers can't tell the difference between simple preserved wood foundation and an ICF basement, so no, they won't pay more when comparing two houses side by side, but that is not why you do ICF in the first place.
Drewski
|
I think the question is about ROI on a house built to the trusses with ICF, not only the foundation.
I think more people look at the flooring and paint colour than how the house was built.
Sent from my iPhone using Tapatalk
|

06-26-2018, 12:16 PM
|
 |
|
|
Join Date: Apr 2018
Location: Calgary
Posts: 1,818
|
|
Quote:
Originally Posted by Sledin
I think the question is about ROI on a house built to the trusses with ICF, not only the foundation.
I think more people look at the flooring and paint colour than how the house was built.
Sent from my iPhone using Tapatalk
|
There's an infill near me with full concrete construction for sale. Same price range as anything else in the Neighborhood.
|

06-26-2018, 12:56 PM
|
 |
|
|
Join Date: Jul 2009
Location: GP AB
Posts: 16,250
|
|
When I sold the first two housed I built here, I had to price them to compete with conventional foundation, they weren't selling with the premium I placed on the foundation. C'est la vie. I still wouldn't build any other way, as I lived in all of them, and the basement is so warm (hydronic heat in floor, with 2" foam under it), that it is actually really usable living space.
Arty was making a comparison between ICF and precast concrete panels, and it is a good comparison. I really like the precast for a lot of the same reasons that he mentioned (though I would argue that a properly done ICF build is not as 'inferior' as maybe he indicated, it's like anything else and needs to be done competently). It is not a very common way at all for residential construction, I've only seen it on commercial buildings. I would definitely look at it if (when?) I chose to build again. But I like a modern, polished concrete look both on the interior and exterior of the house. With lots of glass, stainless, and some wood beams. Mmmmm......like.
__________________
'Once the monkeys learn they can vote themselves a banana, they'll never climb another tree.'. Robert Heinlein
'You can accomplish a lot more with a kind word and a gun, than with a kind word alone.' Al Capone
|

06-26-2018, 02:51 PM
|
|
|
Join Date: Jul 2012
Location: one Fort or another
Posts: 768
|
|
I was mainly getting at the use of precision-built long panels to span several storeys at one time (bsmt, main, second fl) when planted on its short edge, or one entire basement or upper wall if laid on its long edge. And mostly when a simple rectangular structure is involved, with limited penetrations through the wall. That's when crane-erected panels start to make sense.
Unfortunately, too much [tract] housing has now gone from simple Frank Lloyd-Wright architecture, to a narrow tiny Herman Munster peaky horror-house style with all sorts of nooks, crannies, recesses, protrusions and peaks to give the fake illusion of size and uniqueness. That won't work with panels.
Commercial buildings mostly have vertical insulated (or even hollowcore) panels attached to a steel support skeleton, where one panel is not much different from the rest. When you need a big simple box that's very strong, quiet, insulated, secure and requires no maintenance. If the panels are pre-stressed rather than just precast, you can reduce the amount of red-iron steel in the frame too. If you downsize all that a bit it can effectively replace a multi-storey ICF structure in a similar configuration, without all the complications and playing around needed on site.
As a pure basement technology though, I'd still prefer precast or even prestressed insulated sandwich panels laid lengthwise if a simple rectangular foundation is needed.
|

06-26-2018, 03:09 PM
|
 |
|
|
Join Date: May 2007
Location: Central Alberta
Posts: 21,399
|
|
Just had a conversation about these. Expensive way to build a wall, inconvenient To finish inside and out. The foam apparently off gasses for ever and we don't know much about the long term stability of the polystyrene. Exposed to the weather, it does deteriorate quickly No reliable way to confirm the forms are completely filled, very operator skill dependent and the horizontal rebar, usually a pair, impede the flow of concrete to the base. Gotta be very careful vibrating them as well. Points of discussion that were raised.
Grizz
__________________
"Indeed, no human being has yet lived under conditions which, considering the prevailing climates of the past, can be regarded as normal."
John E. Pfeiffer The Emergence of Man
written in 1969
|

06-26-2018, 03:17 PM
|
 |
|
|
Join Date: Jan 2012
Location: 204
Posts: 5,450
|
|
I would say they’re more convenient to finish on the inside.
Skip the insulation and vapour barrier step, and screw drywall right to it.
__________________
"I like to quote my own quotes" ~ Dewey Cox
|

06-26-2018, 03:39 PM
|
 |
|
|
Join Date: Jul 2009
Location: GP AB
Posts: 16,250
|
|
I agree with you on all points Arty, it is a great way to build, and I suspect we will see more instances of pre-stressed and precast being used for residential in the future. I also really like the 'footing to truss' simplicity of it.
I've never priced them out, how do they compare to ICF builds?
__________________
'Once the monkeys learn they can vote themselves a banana, they'll never climb another tree.'. Robert Heinlein
'You can accomplish a lot more with a kind word and a gun, than with a kind word alone.' Al Capone
|

06-26-2018, 04:59 PM
|
|
|
Join Date: Jul 2012
Location: one Fort or another
Posts: 768
|
|
Haven't quoted out panels vs ICF exactly yet, as am still poking/tweaking a house design and resolving details. Locally, Burnco does panels and I've worked with Sterling contacts occasionally in past unrelated jobs needing a crane. You'd need a bit of common steel framing to attach panels to (lots of structural steel suppliers in Edm), a structural engineer to review/modify and stamp any of your CAD stuff, ironworkers, welders and swampers. Those would be my first contact points for panel structure quotes.
One of the key details which needs final resolution is weather-sealing vertical panel edges, especially below grade. As you can imagine, concrete and steel goes through a significant expansion cycle from mid-summer heat (maybe 100F at surface) to minus 60 in worst case. So the neoprene caulking needs to withstand a calculated amount of movement between panels and not become brittle, or some alternative needs to be found; maybe just weld edge tabs together which are cast into the panel and seal the welds. This is all very common and not new, but solid spec and historical data needs to be found to base calculations on to keep all the engineering disciplines and permitting depts happy.
Another detail is the flooring and roof in a concrete walled structure. When you have something as strong as a reinforced concrete box to support your floors, you can put in a very strong long-span diaphragm both on the main and second floors using hollowcore or steel trusses with a topping. No interior walls or posts needed. However, you cannot have a projection through the floor which breaks one prestressed hollowcore into segments but not another, unless equally supported. That's because the deflection under load would be different between one panel and another beside it. So then all segments would have to be broken up equally and/or supported from side-to-side across all ends using a W-beam or other construct. That impacts the layout of the house to a point, but still allows much more open space than usual.
Then we get to the roof. Given a tornado-proof wall, why not a strong roof too? That might be based either on long-span hollowcore bearing end-wall to end-wall along a shallow gable pitch with only small penetrations for venting and chimney, or on several one-piece castings bearing side-wall to side-wall. Maybe based on the hyperbolic arch which the architect Gaudi was so fond of. All old technology, used many times in public or commercial structures in many countries over the years. But the calculations still need to be done. Then all other related prescriptive aspects in the ABC need to be reviewed and checked off too.
If hollow-core is used on the main floor, why not a garage over a full basement, with a service pit under the vehicle? Maybe a little hoisting crane coming up through a common shaft to haul furniture, appliances, groceries or tools with? How about off-grid electrical, with windmills or falling-water generators; backup gensets, maybe 208V 3-phase to shop areas, internal crane and a/c just for giggles. Details, details...
|

06-26-2018, 05:23 PM
|
 |
|
|
Join Date: Jul 2009
Location: GP AB
Posts: 16,250
|
|
Arty....you officially just made my head spin a bit...  But I certainly appreciate your insight into it, as it is something that I have looked at but certainly not to the depth you obviously have. If you proceed with this, keep me posted, pics, maybe a tour at some point? I've been involved in more conventional construction for so many years, that this actually is interesting to me. TC
__________________
'Once the monkeys learn they can vote themselves a banana, they'll never climb another tree.'. Robert Heinlein
'You can accomplish a lot more with a kind word and a gun, than with a kind word alone.' Al Capone
|

06-26-2018, 05:29 PM
|
 |
|
|
Join Date: Feb 2009
Location: Beaverlodge
Posts: 1,859
|
|
Need 209 to speak up as I know he is the middle of big build with icf as we speak
Sent from my iPhone using Tapatalk
|

06-26-2018, 06:24 PM
|
 |
|
|
Join Date: Apr 2018
Location: Calgary
Posts: 1,818
|
|
Quote:
Originally Posted by Arty
Haven't quoted out panels vs ICF exactly yet, as am still poking/tweaking a house design and resolving details. Locally, Burnco does panels and I've worked with Sterling contacts occasionally in past unrelated jobs needing a crane. You'd need a bit of common steel framing to attach panels to (lots of structural steel suppliers in Edm), a structural engineer to review/modify and stamp any of your CAD stuff, ironworkers, welders and swampers. Those would be my first contact points for panel structure quotes.
One of the key details which needs final resolution is weather-sealing vertical panel edges, especially below grade. As you can imagine, concrete and steel goes through a significant expansion cycle from mid-summer heat (maybe 100F at surface) to minus 60 in worst case. So the neoprene caulking needs to withstand a calculated amount of movement between panels and not become brittle, or some alternative needs to be found; maybe just weld edge tabs together which are cast into the panel and seal the welds. This is all very common and not new, but solid spec and historical data needs to be found to base calculations on to keep all the engineering disciplines and permitting depts happy.
Another detail is the flooring and roof in a concrete walled structure. When you have something as strong as a reinforced concrete box to support your floors, you can put in a very strong long-span diaphragm both on the main and second floors using hollowcore or steel trusses with a topping. No interior walls or posts needed. However, you cannot have a projection through the floor which breaks one prestressed hollowcore into segments but not another, unless equally supported. That's because the deflection under load would be different between one panel and another beside it. So then all segments would have to be broken up equally and/or supported from side-to-side across all ends using a W-beam or other construct. That impacts the layout of the house to a point, but still allows much more open space than usual.
Then we get to the roof. Given a tornado-proof wall, why not a strong roof too? That might be based either on long-span hollowcore bearing end-wall to end-wall along a shallow gable pitch with only small penetrations for venting and chimney, or on several one-piece castings bearing side-wall to side-wall. Maybe based on the hyperbolic arch which the architect Gaudi was so fond of. All old technology, used many times in public or commercial structures in many countries over the years. But the calculations still need to be done. Then all other related prescriptive aspects in the ABC need to be reviewed and checked off too.
If hollow-core is used on the main floor, why not a garage over a full basement, with a service pit under the vehicle? Maybe a little hoisting crane coming up through a common shaft to haul furniture, appliances, groceries or tools with? How about off-grid electrical, with windmills or falling-water generators; backup gensets, maybe 208V 3-phase to shop areas, internal crane and a/c just for giggles. Details, details...
|
Precast panels with steel embedments to allow full seam welding work well. We use them for large tank containment berms. Should easily translate for any purpose with some basic engineering. Concrete expansion is minimal compared to many other materials. Cost prohibithive right now due to minimal usage, but that could obviously change..
|

06-26-2018, 07:01 PM
|
 |
|
|
Join Date: Dec 2011
Location: Central Kootenays BC
Posts: 432
|
|
We've been building exclusively with ICF for the past 12 years(approximately 2-3 houses per year plus my own), they are a pleasure to work with compared to traditional cribbing methods. The concrete used to fill the forms is not "watery' it has a plasticizing additive making it flow without changing the strength and somewhat reducing the hydraulic pressure at the base of the forms. Insulation on the outside reduces thermal bridging and the insulation on the inside keeps the warm where it's supposed to be, If you're looking for a thermal mass in regards to passive solar you're better off with concrete floors and a mass center of the house. Another advantage is the sound damping qualities of both concrete and styrofoam. As far as finishing goes it's easy just screw the drywall to the foam on the inside and we usually put 1/2 plywood over the ICF or strap it to create a rain screen.
We've just started to build complete homes out of ICF, mainly due to price of lumber and energy costs. Labour costs are significantly less as well.
|

06-26-2018, 07:03 PM
|
 |
|
|
Join Date: Jul 2010
Location: Edmonton
Posts: 11,858
|
|
There is another, more flexible (from a design perspective), and more cost effective method - the one we use for commercial projects large and small here in North America and for many many large projects and even small homes in Europe.
We all understand how ICF's work and even how un-insulated lightweight foundation walls are formed and shored. A crew of 2-3 guys can form up an average sized home in an easy day. No machinery or equipment needed. Form it up, and call the concrete truck.
For Floors/Ceilings - The system is called Aluma Dek. 2-3 guys in less than a day can form up (errect and place) a floor in your home. Again, no machinery needed, no special tools and you call the concrete truck. The system also allows you to "bow" (forming a pre-stressed floor) in any larger span as required with a simple "twist" of the adjustable drop heads/jacks.
https://www.youtube.com/watch?v=TjwIdXH5w8A
We rents lots of equipment here in Edmonton and Calgary and can recommend an appropriate local contractor to come out for a day or two and set you up and manage your pour.
We can even do your engineering drawing for you if needed.
Just another option for you.
Concrete is going to be more expensive compare to conventional framing/foundation work - but the results are a far stronger, more energy efficient home.
|

06-26-2018, 08:02 PM
|
|
|
Join Date: Jul 2010
Location: Rocky Mnt House
Posts: 936
|
|
Another consideration is that you must finish your basement right away with icf. Or at least put all the drywall on. Or your fire insurance is null and void. So if you were thinking of building and you wanted to finish the badment in a few years to save some cash. Don't
Was a big shock to a few close friends that built. And one that did a icf bassment and put a rtm on it.
The insurance company said the foam is flamible and would not cover it until drywall was up
|

06-26-2018, 08:22 PM
|
|
|
Join Date: Jul 2012
Location: one Fort or another
Posts: 768
|
|
EZM - What you're presenting is an erection aid for a poured-concrete diaphragm floor. That's OK as far as it goes, but my immediate concern is the performance of the finished floor regardless of the means used to build it.
An homogeneous diaphragm works in 2+1 dimensions, where everything would be in tension (not compression) from the top surface downward, if perfectly flat or bowed downward; where the perimeter is all in one horizontal plane. The outside perimeter of the diaphragm is pulled inward as the weight presses downward. That won't work for concrete, as it has very little strength in tension. That is one reason why pre-stressed tension cables are installed into hollowcore and prestressed panels.
As you mention I believe, when you put progressively more upward initial 'bow' into it, it can gradually support more weight as the degree of bow increases. First it's own weight and then beyond, as it transforms into a compressive arc structure. Weight pressing down in the middle translates into force pushing out this time at the perimeter (as well as down at the perimeter).
The problem appears first, that a solid 14" thickness is mentioned which is very heavy, being not hollow. You'd need a significant arc and very strong perimeter wall just for the floor to support itself. The second problem is by the time a high enough arc is achieved (either cylindrical or hyperbolic) to support nominal residential weights mentioned in the ABC over a span 5 or 10 meters +, you'd probably be way beyond any semblance of a flat floor. More like the dome roof of the Roman Pantheon.
So, what span widths are usually achieved using the diaphragm support you've mentioned, how much bow is used, what is the nature of the diaphragm, how thick is it, and what weight can it typically support? Also of interest is what effect cutouts in the diaphragm would have, to allow for staircases for example.
|

06-26-2018, 10:16 PM
|
|
|
Join Date: Nov 2017
Posts: 49
|
|
, one thing I noticed is the fancier the electrical in the house the less insulation left on the walls especially the kitchen areas.they must spray foam after?
|

06-26-2018, 10:22 PM
|
 |
Moderator
|
|
Join Date: Feb 2015
Posts: 7,675
|
|
Quote:
Originally Posted by Twisted Canuck
I've never priced them out, how do they compare to ICF builds?
|
It may suggest something that I'd be willing to bet you've never seen a pre-cast house but IFC homes, at lease homes utilizing IFC basements, are relatively common.
|

06-26-2018, 10:40 PM
|
|
|
Join Date: Jul 2012
Location: one Fort or another
Posts: 768
|
|
Quote:
Originally Posted by Trochu
It may suggest something that I'd be willing to bet you've never seen a pre-cast house but IFC homes, at lease homes utilizing IFC basements, are relatively common.
|
http://www.aboutforeverhome.com/about/
http://www.cpci.ca/en/about_us/proje.../january_2007/
Residential housing is very conservative; people generally don't like anything unfamiliar either on the builder or buyer side, in any particular area, unless there is a compelling reason to change. Precast has been around for a long time in a lot of places however.
|

06-27-2018, 12:49 AM
|
|
|
Join Date: Sep 2007
Posts: 2,380
|
|
http://www.ottawaicf.com/icf-projects1.html
I worked on this home. At the time it was leading the pack.
I have worked on 5 ICF houses. Full foundation to ceiling. 3 of those in Ab.
They are the best way to go if done right.
|

06-27-2018, 06:19 AM
|
 |
Moderator
|
|
Join Date: Feb 2015
Posts: 7,675
|
|
Quote:
Originally Posted by Arty
|
I should have clarified, seen one in Canada.
|

06-27-2018, 07:20 AM
|
 |
|
|
Join Date: Jul 2010
Location: Edmonton
Posts: 11,858
|
|
Quote:
Originally Posted by Arty
EZM - What you're presenting is an erection aid for a poured-concrete diaphragm floor. That's OK as far as it goes, but my immediate concern is the performance of the finished floor regardless of the means used to build it.
An homogeneous diaphragm works in 2+1 dimensions, where everything would be in tension (not compression) from the top surface downward, if perfectly flat or bowed downward; where the perimeter is all in one horizontal plane. The outside perimeter of the diaphragm is pulled inward as the weight presses downward. That won't work for concrete, as it has very little strength in tension. That is one reason why pre-stressed tension cables are installed into hollowcore and prestressed panels.
As you mention I believe, when you put progressively more upward initial 'bow' into it, it can gradually support more weight as the degree of bow increases. First it's own weight and then beyond, as it transforms into a compressive arc structure. Weight pressing down in the middle translates into force pushing out this time at the perimeter (as well as down at the perimeter).
The problem appears first, that a solid 14" thickness is mentioned which is very heavy, being not hollow. You'd need a significant arc and very strong perimeter wall just for the floor to support itself. The second problem is by the time a high enough arc is achieved (either cylindrical or hyperbolic) to support nominal residential weights mentioned in the ABC over a span 5 or 10 meters +, you'd probably be way beyond any semblance of a flat floor. More like the dome roof of the Roman Pantheon.
So, what span widths are usually achieved using the diaphragm support you've mentioned, how much bow is used, what is the nature of the diaphragm, how thick is it, and what weight can it typically support? Also of interest is what effect cutouts in the diaphragm would have, to allow for staircases for example.
|
I will answer you question/respond to your comments in general terms - you ask some good and thoughtful questions. Let me try to add a few comments ...... the engineering of concrete structures (and more appropriately sub structures within a building) and weather they use "tension" or "compression" depends on what you are building and how it "should" be engineered and designed.
Most structures will employ both theories to different parts when designed.
Our company globally engineers and designs more buildings, parkades, sky scrappers, dams, bridges, apartment blocks and residential units than all of our competitors combined. Most of these structures have stair wells, elevators cores, cantilevers, etc... so I would be very comfortable in saying "they thought of that" or at some point "tried that". In Europe they use far less concrete and the engineering, as a result, needs to be more precise as a result.
A 2 story home is a piece of cake. You will not require cables, or any other significant element of "tension" in this application as the floors will be keyed into the wall forms and the pours are staged and equipment is cycled to ensure as you go up to the next floor pretty easily. It's literally lego building.
If you have a large span on an open floor, and wish to pour a thinner floor, the compression (bow) you put into your forming, is there to ensure that the weight of the concrete settles into a flat position - nothing else. (Keep in mind this is for a large unsupported slab, with a thin pour, over a long span). Most residential structures will not have this requirement - but if they did - it would be very quick and easy to form up the floors using simple tools (like a laser) and twisting the jacks/drop heads into the desired potion.
Either way - the force this static and lateral load applies to the outside walls is very little considering the static and aggregate load of the thicker wall forms and columns.
In residential applications, like what we are talking about here, these theoretical elements are negligible as you are generally pouring 2-3 times more concrete that is really required to build these smaller structures to be safe/sound/stable for the life of the building.
Last edited by EZM; 06-27-2018 at 07:33 AM.
|

06-27-2018, 09:15 AM
|
|
|
Join Date: Aug 2007
Location: Magrath, Alberta
Posts: 1,914
|
|
Me and the wife built our forever ICF house 13 years ago, footings to rafters. At the time it was about 10 grand to go ICF over stick build but it was money well spent. Slab on grade with infloor heat in house and garage. Very quite and cheep to heat..
Jim..
|
Posting Rules
|
You may not post new threads
You may not post replies
You may not post attachments
You may not edit your posts
HTML code is Off
|
|
|
All times are GMT -6. The time now is 04:16 PM.
|